plc control relay: the heart of automated control systems
Release time:2025-05-24 19:06:12
Programmable Logic Controllers (PLCs) have become a cornerstone in industrial automation, and one of the critical components that enhances their functionality is the PLC control relay. Relays serve as the intermediary between the PLC and other electrical components in an automated system. They offer an effective method for controlling the operation of machines, systems, and processes by switching high-power electrical circuits with low-power signals from the PLC. In this article, we will explore the working principle of PLC control relays, their importance in automation, and the benefits they bring to various industries.
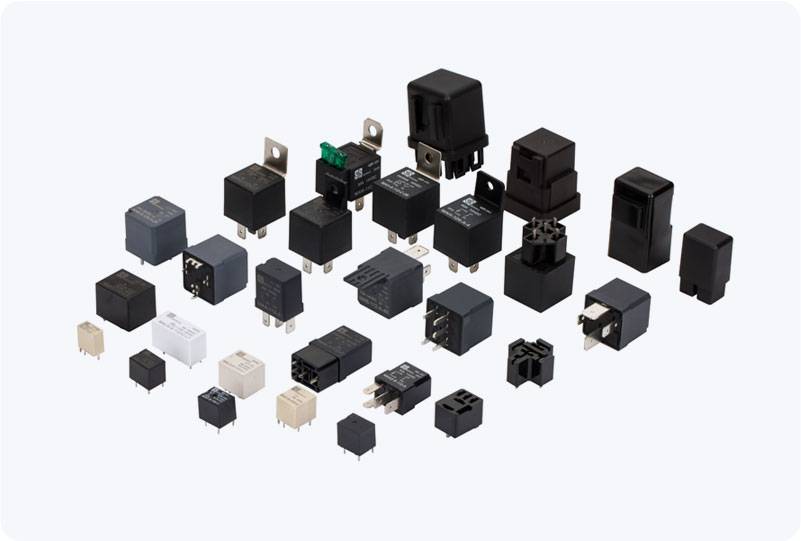
The Basics of PLC Control Relays
A PLC control relay is a mechanical or solid-state device used to control circuits within automated systems. It is activated by a signal from the PLC, which can then open or close the relay’s contacts, ultimately controlling the flow of electricity to other components. The most common application of relays in PLCs is to switch motors, lights, valves, and other equipment that require higher voltage or current than the PLC can directly control.
Relays are often classified into two categories: mechanical relays and solid-state relays. Mechanical relays use an electromagnet to open or close contacts within the relay, whereas solid-state relays use semiconductor components to achieve the same function without moving parts. Both types of relays have their advantages, depending on the application. Mechanical relays are reliable and simple to design, while solid-state relays are more durable and capable of handling higher switching speeds.