power relay contact welding solution: enhancing reliability and performance in electrical systems
Release time:2025-06-29 04:34:36
Power relays are essential components in modern electrical systems, enabling the control of high-current circuits with low-power signals. They are widely used in a variety of applications, from automotive and industrial machinery to home appliances. However, one common issue that affects the reliability of power relays is contact welding, which can lead to malfunction, performance degradation, and even complete failure. This article explores the causes of power relay contact welding and discusses the solutions available to address this problem, ensuring enhanced performance and longevity of electrical systems.
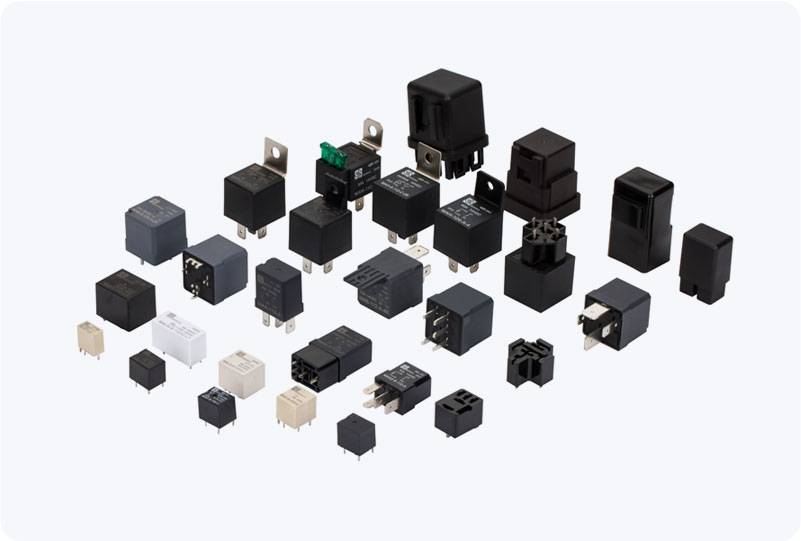
Understanding Power Relay Contact Welding
Contact welding occurs when the electrical contacts within a relay become fused due to high current or excessive arcing during the switching process. When a relay switches on or off, an electrical arc can form at the point where the contacts meet, especially if the current being switched is high or the contacts are not sufficiently robust. Over time, the constant exposure to these electrical arcs can cause the contact points to fuse or weld together, effectively rendering the relay inoperable.
This issue is particularly problematic in high-power applications where relays are tasked with controlling large currents. The consequences of contact welding can range from poor system performance to complete failure, which can lead to costly repairs and downtime. Therefore, finding effective solutions to prevent or minimize contact welding is crucial for maintaining the reliability of electrical systems.